Aspect ratio estimated to be >100 based on TEM.
Aluminium oxide (Al2O3) is a metal oxide based engineered nanosized material that is used in a variety of industrial applications. It can be prepared by the hydrolysis of the alkoxide of Al2O3 and calcinating the particles in the presence of stabilizing agents.
Aluminum oxide is a white odorless crystalline powder. Water insoluble. Properties (both physical and chemical) vary according to the method of preparation; different methods give different crystalline modifications. The variety formed at very high temperature is quite inert chemically.
Aluminum oxide has a chemical formula Al2O3. It is amphoteric in nature, and is used in various chemical, industrial and commercial applications. It is considered an indirect additive used in food contact substances by the FDA.
An oxide of aluminum, occurring in nature as various minerals such as bauxite, corundum, etc. It is used as an adsorbent, desiccating agent, and catalyst, and in the manufacture of dental cements and refractories.
Alumina
CAS No.: 1344-28-1
Cat. No.: VC20975380
Molecular Formula: Al2O3
Molecular Weight: 101.961 g/mol
* For research use only. Not for human or veterinary use.
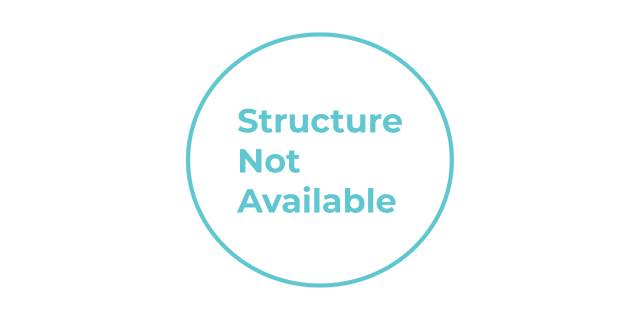
Specification
CAS No. | 1344-28-1 |
---|---|
Molecular Formula | Al2O3 |
Molecular Weight | 101.961 g/mol |
IUPAC Name | dialuminum;oxygen(2-) |
Standard InChI | InChI=1S/2Al.3O/q2*+3;3*-2 |
Standard InChI Key | PNEYBMLMFCGWSK-UHFFFAOYSA-N |
Impurities | Sodium is the main component of the process solution and is also the largest contaminant of the product. ... Gallium is a ubiquitous component of aluminous ores. Its chemistry is similar to that of aluminum, so it accumulates in Bayer process solutions until an equilibrium is reached at about 0.2 g/L. The gallium content of Al2O3 is a linear function of the gallium concentration in the solution. ... Silicon is a component of many aluminum alloys, yet the specification for Al2O3 is less than 0.02% SiO2. ... Potassium is undesirable in the Al2O3 because it may destroy the graphite in Hall-Heroult cells by intercalation, i.e., it diffuses between the layers of the graphite structure, thus expanding its volume. Although it is soluble in Bayer solutions, there has not been a recorded instance of K2O concentrations becoming high enough to affect the Al2O3 quality.... Iron(III)oxide (Fe2O3) as an impurity in Al2O3. ... Calcium also is a common impurity. |
SMILES | [O-2].[O-2].[O-2].[Al+3].[Al+3] |
Canonical SMILES | [O-2].[O-2].[O-2].[Al+3].[Al+3] |
Boiling Point | 5396 °F at 760 mm Hg (NIOSH, 2016) 2977 °C 3000 °C 5396°F |
Colorform | White crystalline powder White powder, balls or lumps or various mesh |
Melting Point | 3632 °F (NIOSH, 2016) 2030 °C 2054 °C 3632°F |
Introduction
Chemical Structure and Fundamental Properties
Alumina, with the chemical formula Al₂O₃, exists naturally in several crystalline forms, with corundum being the most common. When formed under special geological conditions, corundum can develop into precious gemstones like sapphires and rubies, whose colors derive from various trace impurities . The most commercially significant form appears as a refined white powder similar in appearance to table salt or granular sugar .
Physical and Chemical Properties
The fundamental properties of alumina demonstrate why it serves as such a versatile industrial material:
Material Advantages
Alumina possesses a remarkable combination of properties that make it indispensable across numerous applications:
-
Excellent electrical insulation characteristics
-
Exceptional hardness and mechanical strength
-
Superior wear and abrasion resistance
-
High thermal conductivity and resistance to thermal shock
-
Relatively low density compared to other high-performance ceramics
-
Resistance to strong acids and alkalis, particularly at elevated temperatures
-
Transparency to microwave radio frequencies
-
High compressive and dielectric strength
-
Precisely controllable thermal conductivity and expansion rates
These properties enable alumina to withstand harsh operating environments where other materials would rapidly deteriorate.
Production and Extraction Methods
The Bayer Process
The primary method for extracting alumina from raw materials employs the Bayer process, a technique developed in the late 19th century that remains the industry standard. This process begins with bauxite ore, found primarily in tropical and subtropical topsoil regions .
The extraction follows several key steps:
-
Crushing of bauxite ore and dissolution in sodium hydroxide solution
-
Conversion of bauxite to sodium aluminate at elevated temperatures
-
Filtration of impurities, particularly red mud (Fe₂O₃)
-
Cooling of the Bayer liquor, causing Al(OH)₃ precipitation while silicates remain in solution
-
Separation of aluminum oxide particles through heating (calcination) at approximately 1100°C
The resulting alumina serves as the feedstock for aluminum metal production and various other applications depending on purity levels and physical characteristics.
Advanced Production Monitoring and Optimization
Recent innovations in alumina production focus on process optimization through data-driven approaches. Research conducted at Zhengzhou Non-ferrous Metals Research Institute demonstrated successful application of machine learning techniques to predict precipitation rates in alumina production .
The study collected equipment and material data over a three-month period from an operational precipitation area in an alumina plant. After pre-processing, researchers established a time-series dataset with 535 data samples. Using dimensional reduction techniques including principal component analysis (PCA), partial least squares (PLS), and Pearson correlation analysis, they identified critical parameters affecting precipitation rates .
Four prediction models were developed and tested:
-
Linear regression (LR)
-
Support vector machine (SVM)
-
Back propagation neural network (BP)
-
Convolution neural network (CNN)
All models achieved coefficients of determination exceeding 0.8 on the testing dataset, with the CNN model utilizing PLS achieving the highest accuracy at 0.9288 . This research represents significant progress toward intelligent production monitoring in alumina manufacturing.
Material Grades and Variations
Specialized Formulations
Precision Ceramics offers three distinct alumina variations under their CeramAlox brand:
-
CeramAlox Ultra Pure: Exceptionally pure (99.95%) alumina with superior mechanical and electrical properties
-
CeramAlox 99.7: High-purity grade for demanding applications
-
CeramAlox 96: Standard grade for general industrial applications
These variations allow manufacturers to select the most appropriate material based on specific performance requirements and cost considerations.
Industrial Applications
Aluminum Production
The predominant use of alumina globally remains the production of aluminum metal through electrolytic reduction. Aluminum, critical for the low-carbon economy transition, depends entirely on alumina as its precursor material .
Ceramics and Refractories
Alumina serves as a fundamental material in the production of technical ceramics, which combine physical and thermal properties to achieve specific performance requirements. These engineered ceramics find applications in mechanical engineering, casting, automotive, textile, electronic, and medical industries .
The material's exceptional heat resistance (functional up to 1500°C) makes it particularly valuable in refractory applications where materials must maintain structural integrity at extreme temperatures. For these applications, alumina's ability to retain strength at high temperatures proves especially advantageous .
Abrasives and Wear-Resistant Components
Alumina's superior hardness and resistance to abrasion make it ideal for industrial abrasive materials and protective coatings. Specific applications include:
-
Shot blast nozzles
-
Precision shafts and axles in high-wear environments
-
Roller and ball bearings
-
Mechanical seals
-
Valve seats
-
Wire and thread guides
The crystalline form of alumina provides exceptional performance in cutting tools and abrasives for precision manufacturing processes .
Electronics and Electrical Applications
Alumina ceramics offer a combination of properties exceptionally well-suited to electronic applications:
-
High temperature electrical insulators
-
High voltage insulators
-
Electronic components and substrates
-
Laser tubes
-
Semiconductor parts
-
Thermocouple tubes
The material's excellent dielectric properties and thermal conductivity allow electronic components to operate reliably in challenging thermal environments.
Biomedical Applications
In the medical field, alumina serves critical functions in implantable devices and prosthetics:
-
Knee and ankle replacements (in combination with polyethylene)
-
Prosthetic dentistry components
-
Reconstructive materials for face and skull bones
-
Antimicrobial applications through alumina-silver nanocomposites
The material's biocompatibility, inertness, and mechanical stability make it particularly valuable for long-term implantation in the human body, where it facilitates smooth osteointegration and bone ingrowth .
Environmental Applications
Recent research has explored alumina's potential in environmental remediation and climate intervention technologies:
Recent Research Developments
Machine Learning in Production Optimization
Significant research advances have emerged in applying artificial intelligence to alumina production. The Bayer process, while well-established, presents challenges in real-time monitoring and optimization due to its complexity, nonlinearity, large inertia, and numerous interdependent factors .
Researchers have demonstrated that machine learning models can accurately predict precipitation rates using production data, potentially transforming process control approaches. This application of data science to traditional manufacturing processes represents a significant step toward intelligent production systems for alumina .
Environmental Impact Assessment
Recent studies have investigated the potential environmental implications of stratospheric alumina particle injection as a solar radiation modification technique. This research quantifies the uncertainty in modeling ozone response to alumina injection, noting that heterogeneous chemistry on alumina particles remains poorly constrained under stratospheric conditions .
The findings indicate that extrapolating limited experimental data to stratospheric conditions leads to uncertainties in heterogeneous reaction rates of nearly two orders of magnitude. Models implementing injection of 5 Mt/yr of 240 nm radius particles show global total ozone depletions ranging from negligible to as large as 9%, depending on assumptions regarding acid interactions on the alumina surface .
Advanced Materials Development
Innovation continues in developing specialized alumina formulations for next-generation applications:
-
Unbreakable glass incorporating alumina components
-
Alumina-silver composite nanoparticles with enhanced antimicrobial properties
-
Alumina-based catalysts for environmental remediation and chemical processing
-
Novel refractory composites for extreme temperature applications These developments continue to expand alumina's utility across industrial sectors, demonstrating the material's ongoing relevance despite its long history of use.
- mass of a compound required to prepare a solution of known volume and concentration
- volume of solution required to dissolve a compound of known mass to a desired concentration
- concentration of a solution resulting from a known mass of compound in a specific volume