Poly(isophorone diisocyanate)
CAS No.: 53880-05-0
Cat. No.: VC16239616
Molecular Formula: C11H16N2O2
Molecular Weight: 208.26 g/mol
* For research use only. Not for human or veterinary use.
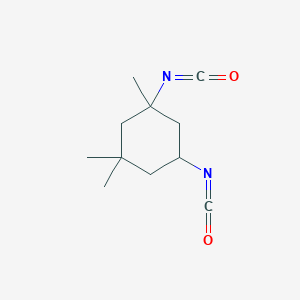
Specification
CAS No. | 53880-05-0 |
---|---|
Molecular Formula | C11H16N2O2 |
Molecular Weight | 208.26 g/mol |
IUPAC Name | 1,5-diisocyanato-1,3,3-trimethylcyclohexane |
Standard InChI | InChI=1S/C11H16N2O2/c1-10(2)4-9(12-7-14)5-11(3,6-10)13-8-15/h9H,4-6H2,1-3H3 |
Standard InChI Key | XIIHTVOIRWYVJC-UHFFFAOYSA-N |
Canonical SMILES | CC1(CC(CC(C1)(C)N=C=O)N=C=O)C |
Introduction
Chemical Structure and Fundamental Properties
Poly(isophorone diisocyanate) is a polyurethane polymer synthesized via the reaction of IPDI with polyols such as polypropylene glycol (PPG) or polyethylene glycol (PEG). IPDI, a cycloaliphatic diisocyanate with the formula , contains two isocyanate groups (-NCO) with differing reactivities: a primary NCO group at the methylene position and a secondary NCO group on the cyclohexane ring . This asymmetry enables controlled polymerization, minimizing side reactions and ensuring linear chain growth .
The polymer’s backbone consists of alternating hard segments (derived from IPDI and chain extenders) and soft segments (from polyols). This microstructure confers tunable glass transition temperatures (), ranging from -60°C to 120°C, depending on the polyol’s molecular weight and the hard-segment content . For instance, IPDI-PPG polyurethanes exhibit values near -50°C, making them suitable for flexible coatings, while IPDI-PEG systems show higher values (up to 80°C) for rigid applications .
Table 1: Key Properties of Poly(isophorone diisocyanate)
Property | Value/Range | Source |
---|---|---|
Density | 1.06–1.12 g/cm³ | |
Glass Transition () | -60°C to 120°C | |
Solubility | Polar aprotic solvents | |
Residual Monomer | <0.1% (post-purification) |
Synthesis and Manufacturing Techniques
Step-Growth Polymerization
Poly-IPDI is synthesized via a two-stage step-growth polymerization process. In the first stage, IPDI reacts with a polyol (e.g., PPG) in a 2:1 molar ratio under catalytic conditions (e.g., dibutyltin dilaurate, DBTL) at 80°C, forming an NCO-terminated prepolymer . The secondary NCO group of IPDI reacts preferentially with the polyol’s hydroxyl groups, leaving the less reactive primary NCO group available for subsequent chain extension . In the second stage, chain extenders like D-isosorbide or water are added to form high-molecular-weight polymers .
Table 2: Optimization Parameters for IPDI Polymerization
Monomer Reduction Strategies
Residual IPDI monomer (<0.1%) is critical for minimizing cytotoxicity in biomedical applications . Advanced techniques include:
-
Thin-Film Evaporation: Removes unreacted IPDI under vacuum at 150°C .
-
Blocked Isocyanate Chemistry: Reacting residual NCO groups with oxime or caprolactam blockers, enabling safer handling and lower unblocking temperatures (90–120°C) .
Reactivity and Chemical Modifications
The differential reactivity of IPDI’s NCO groups allows precise control over polymer architecture. Kinetic studies using matrix-assisted laser desorption ionization mass spectrometry (MALDI-MS) reveal that the secondary NCO group reacts 3–5 times faster with hydroxyl groups than the primary NCO group . This selectivity enables the synthesis of linear prepolymers with minimal branching, as demonstrated by the dominance of α,ω-diisocyanate oligomers in MALDI spectra .
Thermal and Mechanical Performance
Poly-IPDI’s thermal stability stems from its cycloaliphatic structure, with decomposition temperatures () exceeding 250°C . Differential scanning calorimetry (DSC) shows distinct endothermic peaks corresponding to hard-segment melting (150–200°C) and soft-segment transitions . Dynamic mechanical analysis (DMA) reveals storage moduli () of 1–3 GPa for coatings, outperforming aromatic polyurethanes in UV resistance .
Industrial and Biomedical Applications
High-Performance Coatings
Poly-IPDI-based coatings dominate aerospace and automotive industries due to their exceptional weatherability. For example, aircraft exterior paints incorporating poly-IPDI resist yellowing under UV exposure for over 10 years, compared to 2–3 years for toluene diisocyanate (TDI) systems .
Biomedical Devices
Biocompatible poly-IPDI formulations, such as PPG-HMDI-isosorbide terpolymers, exhibit <5% cytotoxicity toward human keratinocytes (HaCaT cells), enabling use in drug-eluting nail lacquers for onychomycosis treatment .
Recent Innovations and Patent Landscape
-
Low-Unblocking-Temperature Compositions: Patent WO2024124426A1 describes IPDI derivatives with methyl-modified cyclohexane rings, reducing unblocking temperatures to 90°C (vs. 130°C conventional) while maintaining optical clarity .
-
Waterborne Polyurethanes: Advances in hydrophilic PEG-IPDI prepolymers enable eco-friendly dispersions with 40% lower volatile organic compound (VOC) emissions .
- mass of a compound required to prepare a solution of known volume and concentration
- volume of solution required to dissolve a compound of known mass to a desired concentration
- concentration of a solution resulting from a known mass of compound in a specific volume