Nitinol
CAS No.: 52013-44-2
Cat. No.: VC1766028
Molecular Formula: Ni14Ti11
Molecular Weight: 1348.2 g/mol
* For research use only. Not for human or veterinary use.
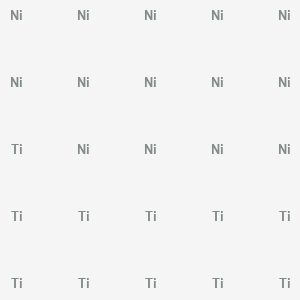
Specification
CAS No. | 52013-44-2 |
---|---|
Molecular Formula | Ni14Ti11 |
Molecular Weight | 1348.2 g/mol |
IUPAC Name | nickel;titanium |
Standard InChI | InChI=1S/14Ni.11Ti |
Standard InChI Key | HLXZNVUGXRDIFK-UHFFFAOYSA-N |
SMILES | [Ti].[Ti].[Ti].[Ti].[Ti].[Ti].[Ti].[Ti].[Ti].[Ti].[Ti].[Ni].[Ni].[Ni].[Ni].[Ni].[Ni].[Ni].[Ni].[Ni].[Ni].[Ni].[Ni].[Ni].[Ni] |
Canonical SMILES | [Ti].[Ti].[Ti].[Ti].[Ti].[Ti].[Ti].[Ti].[Ti].[Ti].[Ti].[Ni].[Ni].[Ni].[Ni].[Ni].[Ni].[Ni].[Ni].[Ni].[Ni].[Ni].[Ni].[Ni].[Ni] |
Introduction
Physical Properties of Nitinol
General Physical Properties
Nitinol possesses a unique set of physical properties that distinguish it from conventional alloys. The material exhibits excellent corrosion resistance similar to that of titanium alloys, making it suitable for applications in corrosive environments, particularly within the human body .
Table 2.1: General Physical Properties of Nitinol
Property | Value |
---|---|
Density | 6.45 g/cm³ (0.233 lb/cu.in) |
Melting point | 1300-1310°C (2370-2390°F) |
Magnetic permeability | <1.002 |
Specific heat | 0.20 cal/g·°C (0.20 BTU/lb·°F) |
Corrosion performance | Excellent |
The thermal properties of Nitinol are particularly interesting because they vary significantly between the austenite and martensite phases. This variation is central to the material's unique behavior and applications.
Thermal Properties
Nitinol exhibits different thermal conductivity and thermal expansion characteristics depending on its phase state. These differences contribute to its functionality in various applications.
Table 2.2: Thermal Properties of Nitinol
Property | Austenite Phase | Martensite Phase |
---|---|---|
Thermal conductivity | 0.18 W/cm·°C (10.4 BTU/ft·hr·°F) | 0.086 W/cm·°C (5.0 BTU/ft·hr·°F) |
Coefficient of thermal expansion | 11.0×10⁻⁶/°C (6.11×10⁻⁶/°F) | 6.6×10⁻⁶/°C (3.67×10⁻⁶/°F) |
Electrical and Magnetic Properties
Nitinol exhibits relatively high electrical resistivity compared to many metals, and its magnetic properties make it suitable for applications where magnetic interference must be minimized.
Table 2.3: Electrical Properties of Nitinol
Property | Value |
---|---|
Electrical resistivity (austenite) | 82×10⁻⁶ Ω·cm |
Electrical resistivity (martensite) | 76×10⁻⁶ Ω·cm |
Magnetic susceptibility (austenite) | 3.7×10⁻⁶ emu/g |
Magnetic susceptibility (martensite) | 2.4×10⁻⁶ emu/g |
Mechanical Properties
The mechanical properties of Nitinol are highly phase-dependent, with significant differences between the austenite and martensite phases. These differences enable its unique mechanical behaviors.
Table 2.4: Mechanical Properties of Nitinol
Property | Value |
---|---|
Ultimate tensile strength | 125,000 psi |
Yield strength, 0.2% offset | 30,000 psi |
Total elongation | 22% |
Elastic modulus (austenite) | 75-83 GPa (10.9×10⁶-12.0×10⁶ psi) |
Elastic modulus (martensite) | 28-40 GPa (4.1×10⁶-5.8×10⁶ psi) |
Yield strength (austenite) | 195-690 MPa (28.3-100.1 ksi) |
Transformation Properties and Mechanisms
Shape Memory Effect
The most remarkable property of Nitinol is its shape memory effect. This phenomenon allows the material to "remember" its original shape and return to it when heated above its transformation temperature, even after substantial deformation . This behavior results from a reversible solid-state phase transformation between crystal structures.
Table 3.1: Transformation Properties of Nitinol
Property | Value |
---|---|
Transformation temperature range | -200 to 110°C |
Latent heat of transformation | 5.78 cal/g |
Transformation strain (for polycrystalline material, single cycle) | max 8% |
Transformation strain (for polycrystalline material, 100 cycles) | 6% |
Transformation strain (for polycrystalline material, 100,000 cycles) | 4% |
Hysteresis | 30 to 50°C |
Phase Transformation Mechanism
Nitinol's unusual properties derive from a reversible solid-state phase transformation known as a martensitic transformation, occurring between two different martensite crystal phases and requiring 69-138 MPa (10,000-20,000 psi) of mechanical stress .
At high temperatures, Nitinol assumes an interpenetrating simple cubic structure referred to as austenite (parent phase). At low temperatures, it spontaneously transforms to a more complex monoclinic crystal structure known as martensite (daughter phase) .
Four critical transition temperatures are associated with the austenite-to-martensite and martensite-to-austenite transformations:
-
Martensite start temperature (Ms): The temperature at which martensite begins to form as the alloy cools from the austenite phase
-
Martensite finish temperature (Mf): The temperature at which the transformation to martensite is complete
-
Austenite start temperature (As): The temperature at which austenite begins to form when the alloy is heated from the martensite phase
-
Austenite finish temperature (Af): The temperature at which the transformation to austenite is complete
The cooling/heating cycle displays thermal hysteresis, typically spanning about 20-50°C (36-90°F), though this range can be modified through alloying and processing techniques .
Superelasticity
In addition to the shape memory effect, Nitinol exhibits superelasticity (also called pseudoelasticity) at temperatures above its austenite finish temperature. In this temperature range, the material can tolerate considerable bending and deformation without taking a permanent set .
Superelasticity allows Nitinol to undergo strains up to 8% and return to its original shape upon unloading, compared to conventional metals which typically can only handle strains of about 0.5% before permanent deformation occurs . This property makes Nitinol particularly valuable in applications requiring flexibility and resilience.
Manufacturing and Processing
Production Methods
The production of Nitinol presents considerable challenges due to the material's reactivity and sensitivity to compositional variations. Conventional hot working directly from arc-melted ingot at temperatures between 700°C and 950°C is the primary forming method . Room temperature working is also possible but requires intermediate anneals at approximately 800°C .
The precise composition of Nitinol is critical, as variations of even 0.1% in the nickel-titanium ratio can significantly alter the transformation temperatures, affecting the material's behavior. This sensitivity necessitates strict quality control during manufacturing processes.
Heat Treatment
Heat treatment plays a crucial role in determining the final properties of Nitinol alloys. Through carefully controlled thermal processing, manufacturers can adjust the transformation temperatures and mechanical properties to suit specific applications. This customization capability is one of the material's major advantages, allowing for tailored performance across diverse operating conditions.
Applications of Nitinol
Medical Applications
The biocompatibility, superelasticity, and shape memory properties of Nitinol make it exceptionally well-suited for medical applications. One significant medical application is in otosclerosis surgery, where Nitinol prostheses have demonstrated superior effectiveness compared to non-Nitinol alternatives .
A meta-analysis comparing Nitinol versus non-Nitinol prostheses in otosclerosis surgery found significant differences in post-operative effectiveness between the two groups, with a combined odds ratio of 2.56 (95% CI 1.38-4.76, p = 0.003) favoring Nitinol . This advantage was particularly pronounced in short-term results (≤ 3 months), where the combined odds ratio was 4.97 (95% CI: 2.47-10.00, p = 0.00001) .
Other common medical applications include:
-
Cardiovascular stents
-
Guidewires for catheterization
-
Orthodontic archwires
-
Orthopedic implants
-
Surgical instruments
The material's ability to maintain constant force over a range of deformations makes it particularly valuable for applications requiring gentle but persistent pressure, such as orthodontic treatments and vascular stents.
Engineering and Industrial Applications
Beyond medicine, Nitinol finds extensive use in various engineering fields:
-
Actuators and motors
-
Coupling devices
-
Sealing components
-
Vibration dampers
-
Temperature sensors and controllers
-
Space and aerospace mechanisms
The material's high fatigue resistance and ability to function as both a sensor and actuator make it valuable for smart systems where mechanical action must respond to environmental changes without external power or control systems.
- mass of a compound required to prepare a solution of known volume and concentration
- volume of solution required to dissolve a compound of known mass to a desired concentration
- concentration of a solution resulting from a known mass of compound in a specific volume