Cumyl dithiobenzoate
CAS No.: 201611-77-0
Cat. No.: VC1885628
Molecular Formula: C16H16S2
Molecular Weight: 272.4 g/mol
* For research use only. Not for human or veterinary use.
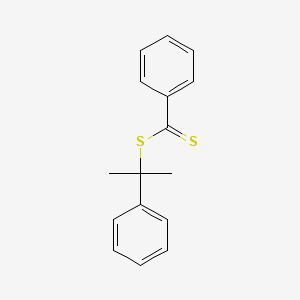
Specification
CAS No. | 201611-77-0 |
---|---|
Molecular Formula | C16H16S2 |
Molecular Weight | 272.4 g/mol |
IUPAC Name | 2-phenylpropan-2-yl benzenecarbodithioate |
Standard InChI | InChI=1S/C16H16S2/c1-16(2,14-11-7-4-8-12-14)18-15(17)13-9-5-3-6-10-13/h3-12H,1-2H3 |
Standard InChI Key | KOBJYYDWSKDEGY-UHFFFAOYSA-N |
SMILES | CC(C)(C1=CC=CC=C1)SC(=S)C2=CC=CC=C2 |
Canonical SMILES | CC(C)(C1=CC=CC=C1)SC(=S)C2=CC=CC=C2 |
Introduction
Chemical Structure and Properties
Cumyl dithiobenzoate (2-phenylpropan-2-yl benzenecarbodithioate) is characterized by a distinctive molecular structure consisting of a cumyl group attached to a dithiobenzoate moiety. This structural arrangement is fundamental to its functionality as a chain transfer agent in RAFT polymerization.
Physical and Chemical Properties
The compound exhibits several distinctive physical and chemical properties that make it valuable for research and industrial applications:
Property | Value |
---|---|
CAS Number | 201611-77-0 |
Molecular Formula | C16H16S2 |
Molecular Weight | 272.4 g/mol |
IUPAC Name | 2-phenylpropan-2-yl benzenecarbodithioate |
Melting Point | 38°C |
Boiling Point | 386.6±35.0°C (Predicted) |
Density | 1.125 g/mL at 25°C |
Flash Point | 104°C |
Physical Form | Liquid |
Color | Dark red-purple |
Stability | Light sensitive; requires storage at 2-8°C |
These properties define the handling requirements and application parameters for cumyl dithiobenzoate in research and industrial settings .
Synthesis Methods
Several synthesis routes have been developed for the preparation of cumyl dithiobenzoate, with variations designed to optimize yield and purity.
Reaction of Dithiobenzoic Acid with α-Methylstyrene
One common synthesis pathway involves the addition of dithiobenzoic acid to α-methylstyrene. This approach represents a direct method for forming the characteristic carbon-sulfur bonds in the target molecule .
Reaction of Sodium Dithiobenzoate with Cumyl Chloride
A more controlled synthesis method involves the preparation of sodium dithiobenzoate followed by reaction with cumyl chloride:
-
Preparation of sodium dithiobenzoate through appropriate precursors
-
Separate preparation of cumyl chloride by reacting cumyl alcohol with hydrochloric acid
-
Reaction of the sodium dithiobenzoate solution with the cumyl chloride in a controlled environment
This method has been reported to achieve high yields of cumyl dithiobenzoate with good purity levels.
Biphasic System Approach
An improved synthetic route involves conducting the reaction in a biphasic system where one phase comprises water. The weight ratio of the aqueous phase to the organic phase typically ranges from 95:5 to 5:95. This approach has demonstrated significant improvements in yield .
The patent literature describes a specific example of this process:
"Cumyl chloride was prepared by shaking 25 g of cumyl alcohol (0.18 mol) and 150 ml of 37% aqueous hydrochloric acid in a separating funnel. The cumyl chloride obtained was extracted into 50 ml of heptane, and the heptane solution was admixed with an excess of anhydrous potassium bicarbonate, in order to neutralize the remaining HCl. The heptane solution including cumyl chloride was added to 250 ml of an aqueous sodium dithiobenzoate solution..."
Role in Reversible Addition-Fragmentation Chain Transfer Polymerization
Cumyl dithiobenzoate functions as a critical mediating agent in RAFT polymerization, a technique that has revolutionized controlled radical polymerization.
Kinetic Parameters
Detailed kinetic studies have provided valuable insights into the behavior of cumyl dithiobenzoate during RAFT polymerization. The key kinetic parameters determined through experimental and modeling studies include:
Parameter | Value | Conditions |
---|---|---|
Addition rate coefficient (kβ) | ~5 × 10^5 L mol^-1 s^-1 | Styrene, 60°C |
Fragmentation rate coefficient (k-β) | ~3 × 10^-2 s^-1 | Styrene, 60°C |
Equilibrium constant (K = kβ/k-β) | ~1.6 × 10^7 L mol^-1 | Styrene, 60°C |
Transfer rate coefficient to cumyl dithiobenzoate | ~3.5 × 10^5 L mol^-1 s^-1 | Styrene, 60°C |
Reaction enthalpy for β-scission | ~50 kJ mol^-1 | High temperature |
These parameters indicate that the equilibrium strongly favors the macroradical RAFT species, which has significant implications for the control of polymerization kinetics .
Applications in Polymer Chemistry
The unique properties of cumyl dithiobenzoate make it valuable for various applications in polymer chemistry, particularly in the synthesis of well-defined polymers.
Polymerization of Styrene
One of the most extensively studied applications of cumyl dithiobenzoate is in the controlled polymerization of styrene. Research has demonstrated that:
-
Cumyl dithiobenzoate effectively controls styrene polymerization even at high temperatures (120-180°C)
-
The resulting polymers show increasing average molecular weight with monomer conversion
-
Polydispersity indices remain below 1.5 at monomer conversions up to 50%
-
No substantial decomposition of the RAFT agent or changes in the polymerization process are observed under these conditions
These characteristics make cumyl dithiobenzoate particularly valuable for industrial applications where high-temperature polymerization is preferred.
Temperature Effects on Polymerization Kinetics
Temperature significantly influences the performance of cumyl dithiobenzoate in RAFT polymerization:
Temperature (°C) | Observation |
---|---|
60 | Significant rate retardation compared to conventional polymerization |
120 | Moderate rate retardation effect |
150 | Reduced rate retardation effect |
180 | Minimal rate retardation effect |
The reduced retardation effect at higher temperatures is attributed to a lower equilibrium concentration of the intermediate RAFT radical .
Applications in Block Copolymer Synthesis
Cumyl dithiobenzoate has proven effective in synthesizing block copolymers with controlled architectures. For example, it has been used to prepare:
-
Poly(4-chloromethylstyrene) and poly(4-chloromethylstyrene)-block-polystyrene through RAFT polymerization
-
Comb polymers with poly(2-methyloxyzoline) side chains, subsequently hydrolyzed to poly(ethyleneimine)
-
Silica materials with controlled morphologies using crystalline aggregates of PEI-bearing comb polymers
These applications demonstrate the versatility of cumyl dithiobenzoate in creating complex polymer architectures.
Comparison with Other RAFT Agents
Comparative studies between cumyl dithiobenzoate and other RAFT agents have revealed important differences in their performance and mechanisms.
Comparison with Cumyl Phenyldithioacetate
Significant differences exist between cumyl dithiobenzoate and structurally similar RAFT agents like cumyl phenyldithioacetate:
Parameter | Cumyl Dithiobenzoate | Cumyl Phenyldithioacetate |
---|---|---|
Rate retardation | Significant | Minimal |
MacroRAFT radical lifetime at 60°C | ~15 seconds | ~1.9 seconds |
Z group | Phenyl | Benzyl |
Equilibrium position | Strongly favors macroRAFT radical | Less shifted toward macroRAFT radical |
These differences arise primarily from the Z group, which affects the stability and lifetime of the macroRAFT radical. The phenyl Z group in cumyl dithiobenzoate provides greater stabilization to the intermediate radical, resulting in a longer lifetime and more pronounced retardation effect .
Thermal Behavior and Stability
The thermal behavior of cumyl dithiobenzoate has significant implications for its application in high-temperature polymerization processes.
Thermal Decomposition
Studies on the thermal decomposition of cumyl dithiobenzoate have provided insights into its stability under various conditions:
-
At temperatures up to 180°C, no substantial decomposition is observed during RAFT polymerization
-
The compound remains stable enough to maintain control over the polymerization process
-
The irreversible termination of the intermediate RAFT radical becomes more significant at higher temperatures
-
The thermal stability makes cumyl dithiobenzoate suitable for high-temperature industrial applications
Current Research and Future Perspectives
Current research on cumyl dithiobenzoate continues to expand its applications and improve understanding of its behavior in various polymerization systems.
Immobilization on Solid Supports
Recent investigations have explored the immobilization of cumyl dithiobenzoate on solid supports, such as silica particles:
-
Cumyl dithiobenzoate has been successfully immobilized via the stabilizing Z-group to nanometer-sized fumed silica particles
-
RAFT polymerizations of styrene and methyl methacrylate performed with immobilized cumyl dithiobenzoate show increasing molecular weights with monomer conversion
-
The approach allows for the production of potentially sulfur-free polymers with controlled molecular weights
This research direction may open new possibilities for the recovery and reuse of RAFT agents in industrial applications.
Mechanistic Studies
Ongoing research continues to refine our understanding of the mechanistic aspects of cumyl dithiobenzoate-mediated RAFT polymerization:
-
The irreversible termination of intermediate RAFT radicals appears to be a more consistent explanation for experimental rate data than slow fragmentation of intermediate radicals
-
Advanced computational and experimental techniques are being applied to further elucidate the kinetic parameters and mechanism
New Applications
Emerging applications for cumyl dithiobenzoate include:
- mass of a compound required to prepare a solution of known volume and concentration
- volume of solution required to dissolve a compound of known mass to a desired concentration
- concentration of a solution resulting from a known mass of compound in a specific volume