Lithium nickel oxide (LiNiO2)
CAS No.: 12031-65-1
Cat. No.: VC20963428
Molecular Formula: LiNiO2
Molecular Weight: 97.7 g/mol
* For research use only. Not for human or veterinary use.
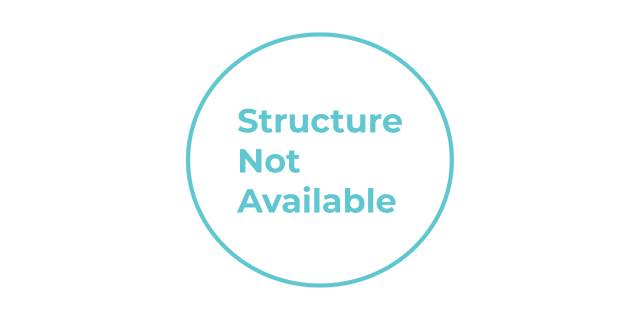
CAS No. | 12031-65-1 |
---|---|
Molecular Formula | LiNiO2 |
Molecular Weight | 97.7 g/mol |
IUPAC Name | lithium;oxido(oxo)nickel |
Standard InChI | InChI=1S/Li.Ni.2O/q+1;;;-1 |
Standard InChI Key | VROAXDSNYPAOBJ-UHFFFAOYSA-N |
Isomeric SMILES | [Li+].[O-][Ni]=O |
SMILES | [Li+].[O-][Ni]=O |
Canonical SMILES | [Li+].[O-][Ni]=O |
Crystal Structure and Fundamental Properties
Crystallographic Structure
Lithium nickel oxide crystallizes in the rhombohedral structure with a space group of R3̅m, similar to its counterpart LiCoO2. In its ideal form, LiNiO2 possesses a layered structure where lithium and nickel occupy distinct crystallographic sites, with lithium ions positioned in the 3a sites and nickel ions in the 3b sites . Oxygen atoms form a framework that coordinates with both the lithium and nickel ions.
The crystal structure can be characterized by its lattice parameters, particularly the a and c constants. Based on experimental measurements, pristine LiNiO2 typically exhibits lattice parameters of a ≈ 2.88 Å and c ≈ 14.2 Å . These parameters are sensitive to synthesis conditions and can vary with the degree of cation mixing and lithium content.
Cation Mixing and Structural Challenges
A significant challenge with LiNiO2 is the phenomenon of cation mixing, where Ni2+ ions migrate into Li+ sites within the crystal structure. This behavior stems from the similar ionic radii of Li+ (0.068 nm) and Ni2+ (0.069 nm), creating a thermodynamic driving force for site exchange. This cation disorder leads to various detrimental effects:
-
Blockage of lithium diffusion pathways
-
Increased impedance during battery operation
-
Structural instability during cycling
-
Reduced reversible capacity
The presence of Ni2+ in lithium layers is quantified as a degree of off-stoichiometry, often represented as Li1-zNi1+zO2, where z indicates the fraction of nickel ions occupying lithium sites . This parameter significantly influences virtually all properties of the material, especially its electrochemical performance.
Electronic and Ionic Transport Properties
The electronic structure of LiNiO2 is characterized by the variable oxidation states of nickel, primarily Ni3+ in the pristine material. During charging (delithiation), nickel undergoes oxidation toward Ni4+, though complete oxidation is rarely achieved due to structural limitations . The electronic conductivity of LiNiO2 is generally higher than that of LiCoO2, which should theoretically benefit its rate capability.
Synthesis Methods and Challenges
Conventional Synthesis Approaches
The synthesis of stoichiometric LiNiO2 presents significant challenges due to the instability of Ni3+ and the tendency for lithium deficiency . Several methods have been developed for LiNiO2 preparation:
-
Solid-state reaction: Involves mixing lithium and nickel precursors (typically carbonates or oxides) followed by high-temperature calcination (700-800°C) under oxygen flow.
-
Sol-gel process: Utilizes solution-based chemistry to achieve more homogeneous mixing of precursors, followed by gelation, drying, and calcination.
-
Co-precipitation method: Involves simultaneous precipitation of lithium and nickel hydroxides from solution before thermal treatment.
Each method faces the fundamental challenge of maintaining the correct stoichiometry while stabilizing the Ni3+ oxidation state. Oxygen partial pressure, temperature, and lithium excess are critical parameters that must be carefully controlled .
Advanced Synthesis Techniques
Recent research has focused on developing improved synthesis methods to address the intrinsic instability of LiNiO2:
Pressurized Oxygen Synthesis: A significant breakthrough involves synthesizing LiNiO2 under elevated oxygen pressure. Even a moderate pressure of 1.7 atm during synthesis markedly improves cycling stability, increasing capacity retention from 59% to 76% after 1000 cycles in full cells with graphite anodes . This improvement is attributed to reduced oxygen vacancy formation and increased Ni3+ content, enhancing structural integrity during cycling.
Table 1: Effect of Synthesis Oxygen Pressure on LiNiO2 Performance
Synthesis Condition | Capacity Retention (1000 cycles) | Key Structural Improvements |
---|---|---|
Ambient Pressure | 59% | Baseline properties |
1.7 atm O2 Pressure | 76% | Reduced oxygen vacancies, Higher Ni3+ content |
Moisture Sensitivity During Processing
A particular challenge in LiNiO2 production is its high reactivity with atmospheric moisture . Exposure to ambient conditions leads to Li+/H+ cation exchange, forming Li1-xHxNiO2 compounds with altered properties . This exchange process causes contraction of the crystal structure, particularly along the c-axis, as demonstrated by both experimental measurements and density functional theory (DFT) calculations.
Table 2: Effect of Atmospheric Exposure on LiNiO2 Lattice Parameters
Sample | H Content (at. %) | a (Å) | c (Å) |
---|---|---|---|
LNO_0h | 0.08 | 2.8776 | 14.2057 |
LNO_9h | 0.28 | 2.8766 | 14.2005 |
LNO_25h | 0.40 | 2.8761 | 14.1988 |
LNO_49h | 0.51 | 2.8755 | 14.1962 |
As shown in the table, increasing hydrogen content correlates with systematic decreases in lattice parameters, particularly the c-axis constant, which directly impacts lithium-ion diffusion kinetics .
Degradation Mechanisms and Stability Issues
Structural Evolution During Cycling
LiNiO2 undergoes several phase transformations during lithium extraction and insertion, contributing to its instability during battery cycling . The material transitions through several phases as lithium content decreases:
-
Initial hexagonal phase (H1)
-
Monoclinic phase (M) at moderate delithiation
-
Second hexagonal phase (H2) at high delithiation
-
Third hexagonal phase (H3) at very high delithiation
These phase transitions involve significant anisotropic lattice changes, including dramatic c-axis expansion during charging that induces mechanical stress and particle cracking .
Surface Reactivity and Electrolyte Decomposition
The surface of LiNiO2 particles exhibits high reactivity with both atmospheric components and battery electrolytes . Key degradation mechanisms include:
-
Formation of lithium carbonate and hydroxide species on particle surfaces
-
Development of rock-salt NiO surface layers approximately 1 nm thick
-
Catalytic decomposition of electrolyte, especially at high states of charge
-
Oxygen release from the lattice at high delithiation levels
These surface reactions contribute to impedance growth, active material loss, and formation of thick solid-electrolyte interphase (SEI) layers that impede lithium-ion transport .
Impact of Li+/H+ Exchange on Electrochemical Properties
The exchange of lithium ions with protons significantly impacts the electrochemical behavior of LiNiO2 . As demonstrated through both experimental and theoretical analyses, increasing hydrogen content correlates with:
-
Higher activation energy for lithium-ion diffusion
-
Decreased rate capability
-
Increased impedance during cycling
-
Reduced reversible capacity
First-principles calculations reveal that H+ incorporation decreases the Li-layer thickness, constricting the diffusion pathway for lithium ions and increasing the energy barrier for lithium migration . This mechanism explains the electrochemical performance degradation observed in moisture-exposed samples.
Performance Enhancement Strategies
Surface Modification Approaches
Surface modification has emerged as an effective strategy to stabilize LiNiO2 and improve its cycling performance. A particularly promising approach involves niobium treatment, which creates a protective surface layer while preserving the bulk structure .
Niobium-treated LiNiO2 demonstrates significantly improved cycling stability, retaining 82% of initial capacity after 500 cycles in full cells with graphite anodes, compared to only 73% for untreated material . The niobium treatment results in the formation of a Li-Nb-O phase coating on primary particles that:
-
Reduces active material loss during cycling
-
Enhances lithium-ion diffusion kinetics
-
Suppresses structural degradation
-
Reduces the formation of nanopore defects during cycling
Other surface modification strategies include aluminum oxide, magnesium oxide, and phosphate coatings, each providing different protective mechanisms against surface-related degradation .
Bulk Doping and Composition Optimization
While pure LiNiO2 presents significant challenges, strategic elemental doping can substantially improve its properties. Common dopants include:
-
Aluminum: Enhances structural stability and thermal safety
-
Manganese: Improves capacity retention and reduces cation mixing
-
Magnesium: Reduces cation disorder and stabilizes the layered structure
-
Titanium: Strengthens the crystal structure and improves cycle life
These dopants generally work by either strengthening the oxygen lattice, reducing cation migration, or both . The success of doping strategies has led to the development of commercial Ni-rich cathodes like LiNi0.8Co0.1Mn0.1O2 (NCM811) and LiNi0.8Co0.15Al0.05O2 (NCA), which represent compromises between the high capacity of LiNiO2 and the stability provided by the dopant elements .
Optimized Cycling Protocols
Beyond material modifications, optimized charging/discharging protocols can significantly extend the usable life of LiNiO2-based batteries . Key strategies include:
-
Limiting the upper cutoff voltage to avoid highly delithiated states
-
Controlling charge/discharge rates, particularly during the initial cycles
-
Implementing appropriate formation protocols to establish stable interfacial layers
-
Temperature management during cycling to minimize side reactions
These operational adaptations can substantially improve the practical performance of LiNiO2, though they often come at the expense of accessible capacity .
Electrochemical Performance Analysis
Capacity and Voltage Characteristics
LiNiO2 offers a theoretical capacity of approximately 275 mAh/g, though practical reversible capacities typically range from 150-200 mAh/g depending on synthesis conditions, cycling parameters, and cell design . The material exhibits a complex voltage profile with multiple plateaus corresponding to phase transitions during lithium extraction and insertion.
Rate Capability and Temperature Dependence
The rate performance of LiNiO2 is strongly influenced by structural factors, particularly cation mixing and lithium layer spacing . Moisture exposure significantly degrades rate capability due to increased activation energy for lithium diffusion, as quantified by both experimental measurements and computational studies .
Temperature has a complex effect on LiNiO2 performance. While elevated temperatures can improve rate capability by enhancing lithium-ion diffusion, they also accelerate side reactions and structural degradation, leading to faster capacity fade .
Long-term Cycling Stability
The cycling stability of LiNiO2 has been significantly improved through advanced synthesis and modification strategies. Recent studies demonstrate that optimized materials can achieve impressive cycle life:
-
Niobium-treated LiNiO2: 82% capacity retention after 500 cycles
-
Oxygen-pressure-synthesized LiNiO2: 76% capacity retention after 1000 cycles
Current Applications and Future Prospects
Research Frontiers and Emerging Solutions
Current research on LiNiO2 focuses on several promising directions:
-
Advanced synthesis protocols: Exploring pressure, temperature, and atmospheric control to minimize defects
-
Novel surface treatments: Developing multifunctional coatings that address multiple degradation mechanisms simultaneously
-
Artificial solid-electrolyte interphase (SEI) engineering: Creating stable interfaces that prevent continuous electrolyte decomposition
-
Computational screening: Using first-principles calculations to identify optimal dopants and surface modifications
The combination of experimental advances and computational insights is accelerating progress toward stable, high-performance LiNiO2-based cathodes .
Integration with Next-generation Battery Technologies
LiNiO2 and its derivatives are being explored for integration with emerging battery technologies:
-
Solid-state batteries: The high energy density of LiNiO2 makes it attractive for pairing with solid electrolytes, though interfacial stability presents challenges
-
Fast-charging systems: Modified LiNiO2 with enhanced rate capability could enable faster charging for electric vehicles
-
Silicon and lithium metal anodes: Pairing with high-capacity anodes to maximize full-cell energy density
These integration efforts face significant challenges but represent potential pathways to dramatic improvements in battery performance .
Mass Molarity Calculator
- mass of a compound required to prepare a solution of known volume and concentration
- volume of solution required to dissolve a compound of known mass to a desired concentration
- concentration of a solution resulting from a known mass of compound in a specific volume