Butyl prop-2-enoate;styrene
CAS No.: 25767-47-9
Cat. No.: VC3892655
Molecular Formula: C15H20O2
Molecular Weight: 232.32 g/mol
* For research use only. Not for human or veterinary use.
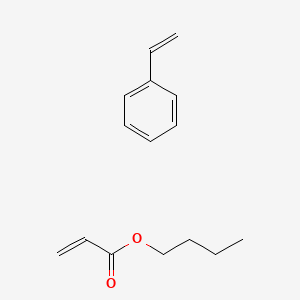
CAS No. | 25767-47-9 |
---|---|
Molecular Formula | C15H20O2 |
Molecular Weight | 232.32 g/mol |
IUPAC Name | butyl prop-2-enoate;styrene |
Standard InChI | InChI=1S/C8H8.C7H12O2/c1-2-8-6-4-3-5-7-8;1-3-5-6-9-7(8)4-2/h2-7H,1H2;4H,2-3,5-6H2,1H3 |
Standard InChI Key | TUZBYYLVVXPEMA-UHFFFAOYSA-N |
SMILES | CCCCOC(=O)C=C.C=CC1=CC=CC=C1 |
Canonical SMILES | CCCCOC(=O)C=C.C=CC1=CC=CC=C1 |
Chemical Structure and Composition
Molecular Architecture
Butyl prop-2-enoate; styrene is a copolymer comprising two primary monomers:
-
Butyl acrylate: An α,β-unsaturated ester () contributing flexibility and low glass transition temperatures ().
-
Styrene: A vinyl aromatic hydrocarbon () imparting rigidity and thermal stability .
The copolymer’s structure arises from radical polymerization, where styrene’s phenyl groups and butyl acrylate’s ester functionalities create a balanced hydrophobic-hydrophilic profile. Fourier-transform infrared (FTIR) spectroscopy confirms covalent bonding between monomers, with characteristic peaks at 1731 cm (C=O stretch of acrylate) and 3100 cm (aromatic C–H stretch) .
Table 1: Key Structural Properties
Property | Value/Description | Source |
---|---|---|
Molecular Formula | ||
Molecular Weight | 232.32 g/mol | |
CAS No. | 25767-47-9 | |
Dominant Functional Groups | Ester (acrylate), Aromatic (styrene) |
Synergistic Effects
The copolymer’s performance stems from monomer synergy. Butyl acrylate’s long alkyl chain reduces brittleness, while styrene’s aromatic rings enhance mechanical strength. Differential scanning calorimetry (DSC) reveals a single between -40°C (pure butyl acrylate) and 100°C (pure polystyrene), tunable via monomer ratios . For instance, a 14 wt.% butyl acrylate formulation increases elasticity by 30% compared to pure styrene polymers .
Synthesis and Polymerization
Emulsion Polymerization
Industrial production predominantly uses emulsion polymerization due to its scalability and control over particle size. The process involves:
-
Initiator Addition: Potassium persulfate or azobisisobutyronitrile (AIBN) generates free radicals.
-
Monomer Feed: Styrene and butyl acrylate are gradually added to aqueous surfactant solutions (e.g., sodium dodecyl sulfate) .
-
Temperature Control: Reactions proceed at 70–90°C, achieving >95% conversion within 2 hours .
Critical parameters include:
-
pH: Maintained at 6–8 to stabilize latex particles.
-
Monomer Ratio: A 3:1 styrene-to-butyl acrylate ratio optimizes adhesive strength.
Bulk Free Radical Polymerization
For lignin-based composites, bulk polymerization at 90°C with benzoyl peroxide initiator incorporates 5–20 wt.% lignin into the copolymer matrix . This method eliminates solvents, reducing environmental impact. Reaction kinetics show 99% styrene conversion within 1.3 hours, with lignin’s hydroxyl groups reacting preferentially with styrene radicals .
Lignin (wt.%) | Shore D Hardness | (°C) | Tensile Strength (MPa) |
---|---|---|---|
0 | 25 | 78 | 12 |
5 | 38 | 82 | 18 |
20 | 69 | 94 | 27 |
These composites exhibit potential as hydrocarbon spill absorbents, with a 15 g/g oil uptake capacity .
Recent Research Advancements
Thermal and Mechanical Optimization
Studies demonstrate that increasing lignin content from 5% to 20% raises the decomposition onset temperature from 220°C to 290°C (thermogravimetric analysis) . Concurrently, Shore D hardness escalates linearly with lignin concentration, making the material suitable for synthetic wood applications .
Environmental Remediation
Sulfonated lignin-styrene-butyl acrylate copolymers show promise in wastewater treatment, achieving 90% removal of cationic dyes (e.g., methylene blue) via electrostatic interactions .
Challenges and Future Directions
While butyl prop-2-enoate; styrene copolymers offer versatility, limitations persist:
-
Volatility: Butyl acrylate monomers require stringent handling due to respiratory irritation risks.
-
Lignin Compatibility: High lignin loads (>20%) cause phase separation, necessitating compatibilizers .
Future research should explore:
-
Green Chemistry: Enzymatic polymerization routes to reduce initiator toxicity.
-
Smart Materials: Stimuli-responsive copolymers for drug delivery or self-healing coatings.
Mass Molarity Calculator
- mass of a compound required to prepare a solution of known volume and concentration
- volume of solution required to dissolve a compound of known mass to a desired concentration
- concentration of a solution resulting from a known mass of compound in a specific volume