Aluminium-nickel
CAS No.: 12635-27-7
Cat. No.: VC0079250
Molecular Formula: AlNi
Molecular Weight: 85.67
* For research use only. Not for human or veterinary use.
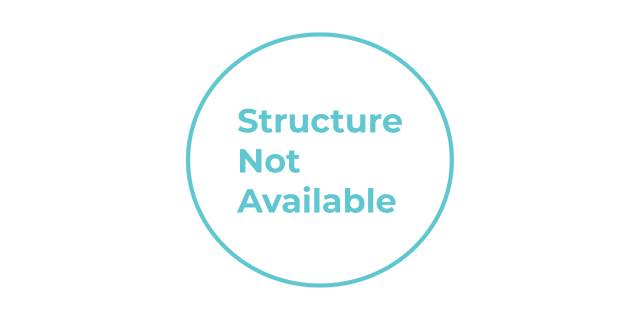
Specification
CAS No. | 12635-27-7 |
---|---|
Molecular Formula | AlNi |
Molecular Weight | 85.67 |
IUPAC Name | aluminum;nickel |
Standard InChI | InChI=1S/Al.Ni |
SMILES | [Al].[Ni] |
Introduction
Chemical Composition and Types
Primary Intermetallic Compounds
Aluminium-nickel primarily refers to two widely used intermetallic compounds:
-
Ni3Al: Contains 75% nickel and 25% aluminum by atomic percentage. It serves as a crucial precipitate in nickel-based superalloys, known as the γ' (gamma prime) phase, providing high strength and creep resistance at elevated temperatures .
-
NiAl: Contains 50% nickel and 50% aluminum by atomic percentage. It features lower density and higher melting temperature than Ni3Al, along with excellent thermal conductivity and oxidation resistance, making it attractive for specialized high-temperature applications .
Other Variations
Besides the two primary compounds, other aluminium-nickel alloys exist, including:
-
Al3Ni2 and Al3Ni, which form during certain processing conditions
-
NiAl3, which may develop in specific aluminum-rich compositions
-
Various commercial compositions are available, including Al-21% Ni-79%, Al-41% Ni-59%, Al-50% Ni-50%, and Al-80% Ni-20%
Crystal Structure and Physical Properties
Crystal Structure
The crystal structures of aluminium-nickel compounds fundamentally influence their unique properties:
-
Ni3Al: Features an L12 crystal structure (Strukturbericht designation) with a lattice parameter of 0.357 nm. In this ordered structure, nickel atoms occupy the face centers of the cubic lattice, while aluminum atoms are positioned at the corners .
-
NiAl: Exhibits a B2 crystal structure with a lattice parameter of 0.2887 nm .
X-ray analysis of the nickel-aluminium system revealed that the α-phase (face-centered cubic solid solution of aluminium in nickel) extends to 89 atomic % of nickel at room temperatures. The α'-phase, corresponding closely to Ni3Al, has a superlattice structure .
Physical Properties
Aluminium-nickel compounds exhibit distinctive physical properties as shown in Table 1:
Table 1: Physical Properties of Ni3Al and NiAl
Property | Ni3Al | NiAl |
---|---|---|
Crystal structure | L12 | B2 |
Lattice parameter a | 0.357 nm | 0.2887 nm |
Density | 7.50 g/cm³ | 5.85 g/cm³ |
Young's modulus | 179 GPa | 294 GPa |
Yield strength | 855 MPa | - |
Melting point | 1,385 °C (1,658 K) | 1,639 °C (1,912 K) |
Thermal expansion coefficient | 12.5×10⁻⁶/K | 13.2×10⁻⁶/K |
Electrical resistivity | 32.59×10⁻⁸ Ω⋅m | 8 to 10×10⁻⁸ Ω⋅m |
Thermal conductivity | 28.85 W/(m⋅K) | 76 W/(m⋅K) |
Mechanical Properties
Strength and Ductility
A significant challenge with aluminium-nickel compounds is their brittleness at room temperature, which limits their structural applications . This brittleness stems from the inability of dislocations to move freely within their highly ordered lattice structures. Several approaches have been investigated to overcome this limitation:
In experimental copper-aluminium-nickel alloys, the Cu-12Al-4Ni alloy exhibited the highest ultimate tensile strength at 595.9 ± 14.2 MPa. Generally, tensile strength increases with higher content of both aluminium and nickel, with aluminium showing a stronger influence on property enhancement .
High-Temperature Performance
The exceptional high-temperature performance of aluminium-nickel compounds is one of their most valuable characteristics:
-
Ni3Al maintains substantial strength up to 0.7-0.8 of its melting temperature, making it highly suitable for applications in extreme thermal environments .
-
NiAl, with its higher melting point and good thermal conductivity, offers excellent oxidation resistance at elevated temperatures .
Research indicates that fabrication methods significantly influence high-temperature performance. Hot pressing has been found to improve the ductility and fracture toughness of nickel aluminide intermetallics, as sintering promotes strengthening mechanisms .
Manufacturing and Processing Techniques
Conventional Methods
Traditional manufacturing methods face challenges due to the high aluminum content and large difference in melting points between nickel and aluminum, which can lead to oxidation or porosity in fabricated components .
The "Exo-melt" process, developed by Oak Ridge National Laboratory in 1996, offers a solution by utilizing the heat generated during the exothermic reaction to melt all constituents rapidly. This process provides approximately 50% savings in both time and energy . It has been employed by several manufacturers, including:
-
Alloy Engineering and Casting Company in Champaign, Illinois
-
United Defense in Anniston, Alabama
-
The BiMac Corporation in Dayton, Ohio
Advanced Processing Techniques
Several advanced processing techniques have been explored for aluminium-nickel compounds:
-
Hot pressing: Improves ductility and fracture toughness of nickel aluminide intermetallics .
-
Self-propagating high-temperature synthesis (SHS): Utilizes exothermic reactions to form compounds rapidly. This can occur in two modes: self-propagating (combustion front) or thermal explosion (throughout the sample simultaneously) .
-
Spark plasma sintering: Creates nickel aluminide materials with enhanced properties through the application of pulsed direct current and pressure .
-
Additive manufacturing: Recently emerged as a preferred method for building intermetallic materials with complex geometries .
-
Electrodeposition: Used to produce coatings with a nickel matrix and aluminum particles. EPMA results for Ni-Al-Si partially reacted at 508°C showed intermetallic phases containing 48.2% Ni, 44.8% Al, and 7.0% Si (atomic percentages) .
Metal-Intermetallic Laminate (MIL) Composites
To overcome brittleness, metal-intermetallic laminate (MIL) composites have been developed. Research has included:
-
Binary nickel-aluminum reaction systems
-
Ternary systems involving aluminum and nickel-chromium alloy
-
Quaternary systems using aluminum and nickel-iron-chromium alloy
For the Ni-Al system, MIL composites of Ni-(Al3Ni2+Al3Ni) and Ni-Al3Ni2 have been successfully fabricated. When using Invar and aluminum, intermetallic phases of Al79Fe16Ni6 and Al84Fe9Ni7 were obtained, while systems using Inconel and aluminum produced Al80Cr3Fe3Ni7Mo and Al85Cr3Fe3Ni7Mo phases .
Applications
High-Temperature Structural Applications
Aluminium-nickel compounds excel in environments requiring high-temperature strength and corrosion resistance:
-
Forging dies and furnace assembly components
-
Turbocharger components, valves, and piston heads for internal combustion engines
-
Jet engine turbine blades manufactured from directionally solidified Ni3Al-based alloys
-
Stainless steels and nickel-containing alloys in the pulp and paper industry, particularly in digesters and oxygen delignification reactors
Coatings and Surface Treatments
The excellent oxidation resistance and thermal properties make aluminium-nickel compounds ideal for protective coatings:
-
Electrodeposited metal matrix-metal particle composite (EMMC) coatings with a nickel matrix and aluminum particles for surface protection
Advanced Technological Applications
Ni3Al-based alloys in the form of thin foils and strips contribute to high-tech devices:
-
Micro Electro-Mechanical Systems (MEMS)
-
Microtechnology-based Energy and Chemical Systems (MECS)
-
Heat exchangers and microreactors
-
Micro-actuators
-
Components of combustion chambers and gaskets for rocket and jet engines
Catalytic Applications
The catalytic properties of aluminium-nickel compounds are utilized in:
-
Catalytic converters
-
Air purification systems for chemical and biological toxic agents
-
Hydrogen production through the decomposition of hydrocarbons
-
Nickel-aluminum flame-sprayed catalysts for various industrial processes
Dental Applications
Research on copper-aluminium-nickel alloys has explored their potential for dental post and core applications. The Cu-9Al-2Ni and Cu-9Al-4Ni alloys demonstrated appropriate modulus of elasticity (113.9 ± 8.0 and 122.8 ± 11.3 GPa, respectively) and 0.2% proof strength (190.8 ± 4.8 and 198.2 ± 3.4 MPa, respectively) that complied with ISO standard requirements (>180 MPa) .
Recent Research and Developments
Alloying and Composite Development
Current research focuses on enhancing properties through alloying and composite development:
-
Composite materials with Ni3Al-based alloys as a matrix, hardened by reinforcements such as TiC, ZrO2, WC, SiC, and graphene
-
The influence of nickel percentage on lattice structure and mechanical properties in Al-Si alloys, showing that the addition of Ni leads to the formation of an intermetallic compound, Al3Ni, which changes the lattice constant and improves hardness
-
Copper-aluminium-nickel alloys with varying compositions (3-12 wt% Al and 0-6 wt% Ni) for specialized applications
Challenges and Future Prospects
Overcoming Brittleness
The most significant limitation of aluminium-nickel compounds is their brittleness at room temperature. Current approaches include:
Biocompatibility and Environmental Considerations
Research on copper-aluminium-nickel alloys has revealed potential concerns:
-
Alloys with high nickel content (6 wt% Ni) showed widespread decolorization zones (5.0-5.9 mm) in cytotoxicity tests
-
Elution of copper decreased when aluminum content increased to 9%, confirming aluminum's role as a tarnish protector
-
The amount of nickel leaching increased with higher nickel content, with the lowest values observed in 6 wt% Al alloys
These findings highlight the need for careful consideration of composition when developing aluminium-nickel alloys for applications involving human contact or environmental exposure.
Cost-Effective Manufacturing
The development of more economical manufacturing processes remains an important goal. While the Exo-melt process has demonstrated significant time and energy savings , further innovations in processing techniques could make aluminium-nickel compounds more economically viable for a broader range of applications.
- mass of a compound required to prepare a solution of known volume and concentration
- volume of solution required to dissolve a compound of known mass to a desired concentration
- concentration of a solution resulting from a known mass of compound in a specific volume