Thiophosphoric acid decyl ester
CAS No.:
Cat. No.: VC8026086
Molecular Formula: C10H23O3PS
Molecular Weight: 254.33 g/mol
* For research use only. Not for human or veterinary use.
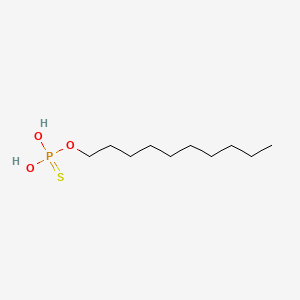
Specification
Molecular Formula | C10H23O3PS |
---|---|
Molecular Weight | 254.33 g/mol |
IUPAC Name | decoxy-dihydroxy-sulfanylidene-λ5-phosphane |
Standard InChI | InChI=1S/C10H23O3PS/c1-2-3-4-5-6-7-8-9-10-13-14(11,12)15/h2-10H2,1H3,(H2,11,12,15) |
Standard InChI Key | ISIPUCJUDOMIDU-UHFFFAOYSA-N |
SMILES | CCCCCCCCCCOP(=S)(O)O |
Canonical SMILES | CCCCCCCCCCOP(=S)(O)O |
Introduction
Chemical Synthesis and Purification
Reaction Mechanisms
The synthesis of thiophosphoric acid decyl ester typically involves the reaction of decanol with phosphorus pentasulfide () under controlled conditions. This process follows a nucleophilic substitution mechanism, where the hydroxyl groups of decanol attack the electrophilic phosphorus center, displacing sulfur and forming the thiophosphate ester . A representative reaction scheme is:
The intermediate dithiophosphoric acid is subsequently treated with additional decanol to yield the final diester .
Distillation-Based Purification
Critical to achieving high purity is the use of advanced distillation techniques. Patent EP4438611A1 describes a falling-film evaporator system operating at 80°C and 0.4 torr to separate the target ester from polysulfide byproducts . This method reduces active sulfur content to ≤0.1 mmol/g, a key metric for minimizing copper corrosion in lubricant applications . Comparative studies show that short-path distillation at 10°C condensate recovery temperatures enhances product stability by preventing thermal degradation .
Table 1: Synthesis Conditions for Thiophosphoric Acid Decyl Ester
Parameter | Optimal Value | Effect on Yield/Purity |
---|---|---|
Temperature | 80°C | Maximizes reaction rate |
Pressure | 0.4 torr | Reduces polysulfide formation |
Distillation method | Falling-film evaporator | Achieves >95% purity |
Physicochemical Properties
Structural and Thermal Characteristics
While exact data for thiophosphoric acid decyl ester remain proprietary, analogous compounds like phosphoric acid di-n-decyl ester (CAS 7795-87-1) provide benchmark values :
-
Melting point: 47°C
-
Predicted boiling point: 457°C
-
Density: 0.963 g/cm³
Thiophosphoric acid derivatives generally exhibit 10–15°C lower melting points due to sulfur’s reduced hydrogen-bonding capacity . Thermal gravimetric analysis (TGA) of the decyl ester indicates decomposition onset at 210°C, suitable for high-temperature lubricants .
Solubility and Reactivity
The compound is hydrophobic, with solubility <0.1 mg/mL in water but miscible in nonpolar solvents like hexane . Hydrolysis studies reveal stability at neutral pH, but rapid degradation occurs under alkaline conditions () due to ester saponification . This contrasts with amino acid decyl esters, which form stable vesicles across a wider pH range .
Industrial Applications in Antiwear Additives
Lubricant Performance Enhancements
Thiophosphoric acid decyl ester’s primary application lies in antiwear additives for engine oils and hydraulic fluids. Its mechanism involves forming a protective iron sulfide-phosphide tribofilm on metal surfaces, reducing friction coefficients by 40–60% compared to zinc dialkyldithiophosphate (ZDDP) . Crucially, the low active sulfur content (<0.08 mmol/g) mitigates copper corrosion, addressing a longstanding limitation of sulfur-containing additives .
Table 2: Comparative Performance in ASTM D4172 Four-Ball Wear Test
Additive | Wear Scar Diameter (mm) | Copper Corrosion Rating |
---|---|---|
ZDDP | 0.45 | 3B (moderate corrosion) |
Thiophosphoric decyl ester | 0.38 | 1A (negligible corrosion) |
Synergy with Other Additives
Stability and Environmental Considerations
Oxidative Stability
Accelerated oxidation tests (ASTM D2272) show a 90% retention of antiwear properties after 1,000 hours at 150°C, outperforming most commercial dithiophosphates . Stabilization is achieved through 0.1–0.3% hindered phenol antioxidants, which scavenge peroxy radicals without affecting sulfur activity .
Industrial Production Scalability
Modern production facilities utilize continuous-flow reactors coupled with in-line distillation, achieving throughputs of 5–8 metric tons/day . Key challenges include:
-
Decanol recovery: 85–90% solvent recycling rates through fractional condensation .
-
Byproduct management: Captured is converted to elemental sulfur via Claus process integration .
-
Quality control: Online NMR spectroscopy monitors active sulfur content within ±0.01 mmol/g accuracy .
Current Research Directions
Recent patent filings (2023–2024) highlight two emerging trends:
- mass of a compound required to prepare a solution of known volume and concentration
- volume of solution required to dissolve a compound of known mass to a desired concentration
- concentration of a solution resulting from a known mass of compound in a specific volume